Overview
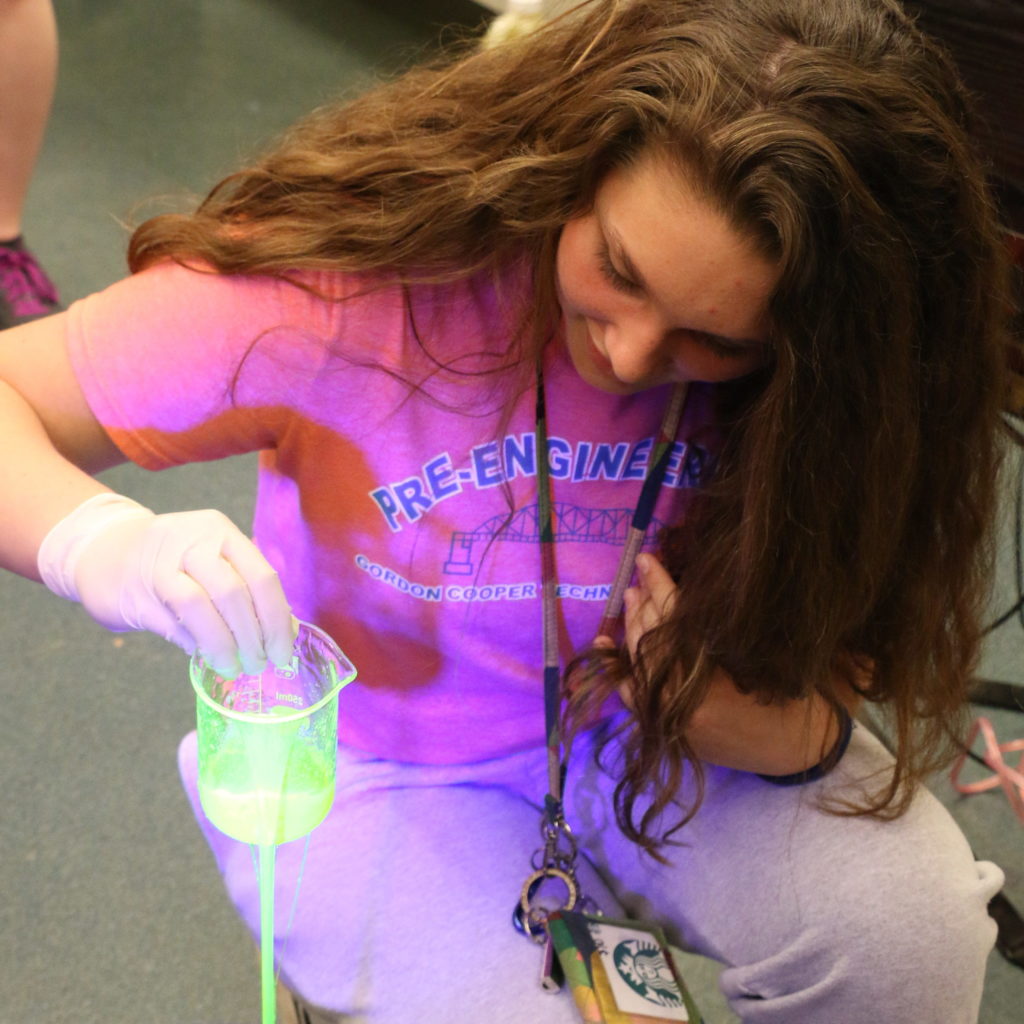
Skin-friction (or viscous) drag is a major contributor to the resistance of objects moving in a fluid. Thus the skin-friction reduction is an ongoing research priority for improved fuel savings and performance of transportation systems. It has been known since the late 1940s that the presence of high molecular weight polymers, even at low concentrations (~10 weight-parts per million, wppm), in the near-wall region of a liquid turbulent flow can reduce the friction drag by 75%. Polymer drag reduction (PDR) has been implemented successfully in various internal commercial fluid flow applications (e.g. sewer systems, fire hoses, oil pipelines, etc.) that are better suited to PDR since dilution is limited. In the absence of polymer degradation, sustained levels of high drag reduction are possible.
On the other hand, external flows applications are limited due to the continual dilution of the polymer solution by entrainment of ambient fluid into the wall region. Consequently, large fluxes of high molecular weight polymer solutions must be injected to maintain a sufficient polymer concentration in the near wall region for effective PDR over long downstream distances. However, high molecular weight polymers are susceptible to flow-induced degradation by chain scission, which decreases the drag reducing effectiveness of the polymer. Moreover, external flow surfaces may be rough, which would accelerate both dilution and degradation. Thus our team studies the diffusion of polymer, mechanical (or flow-assisted) degradation, and the resulting modification of the velocity profiles due to reduction in skin-friction.
2010 America’s Cup – The Slick System

Sailing Anarchy – The Slick System
Remember the tarp over the rear beam?! It covered a holding tank located on the back center of the rear beam during testing. In the holding tank was a mixture of the polymer and alcohol, and it was pumped out of two slits in each float…once it exited from under the hull, it mixed with the [water] and dissipated with no trace in the boat’s wake.
Now here’s the mindblower: When the system was on, it provided a [velocity made good] increase upwind of almost three knots! That is upwind velocity made good, not just boatspeed.
Mechanical Degradation
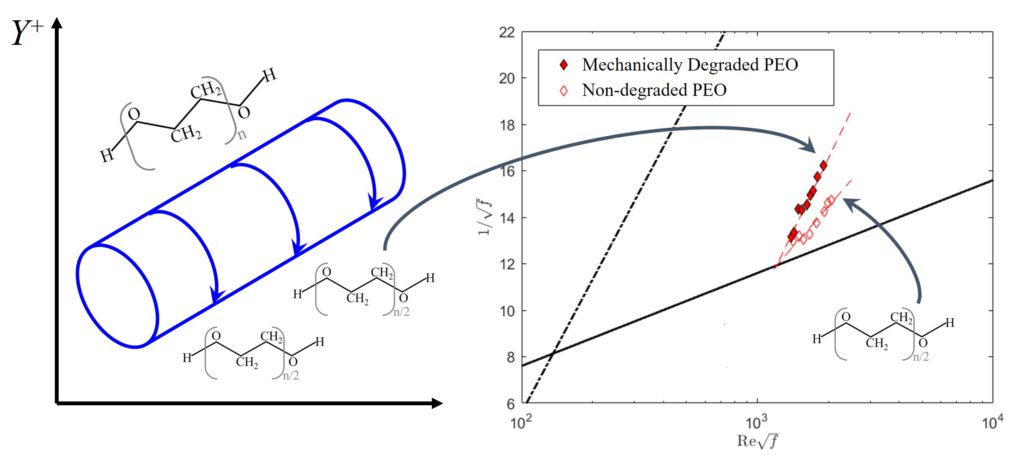
One of the primary limiting factors for advancing PDR to external flows (as well as expanding internal flow applications) is polymer degradation from chain scission induced from high shear rates. This problem is exasperated by the fact that polymers are generally more efficient at reducing drag (i.e. require lower concentrations to achieve a desired drag reduction) the longer the polymer chain, but the longer the polymer chain the more susceptible it is to chain scission. Internal flows have historically avoided this problem by using stiffer polymers (e.g. polyacrylamides). Conversely, external flows have focused primarily on high molecular weight polyethylene oxide. As a result polymer degradation has had a significant impact on PDR external applications and even the ability to study PDR within turbulent boundary layers.
Near-Wall Velocity Profiles in a Polymer Ocean
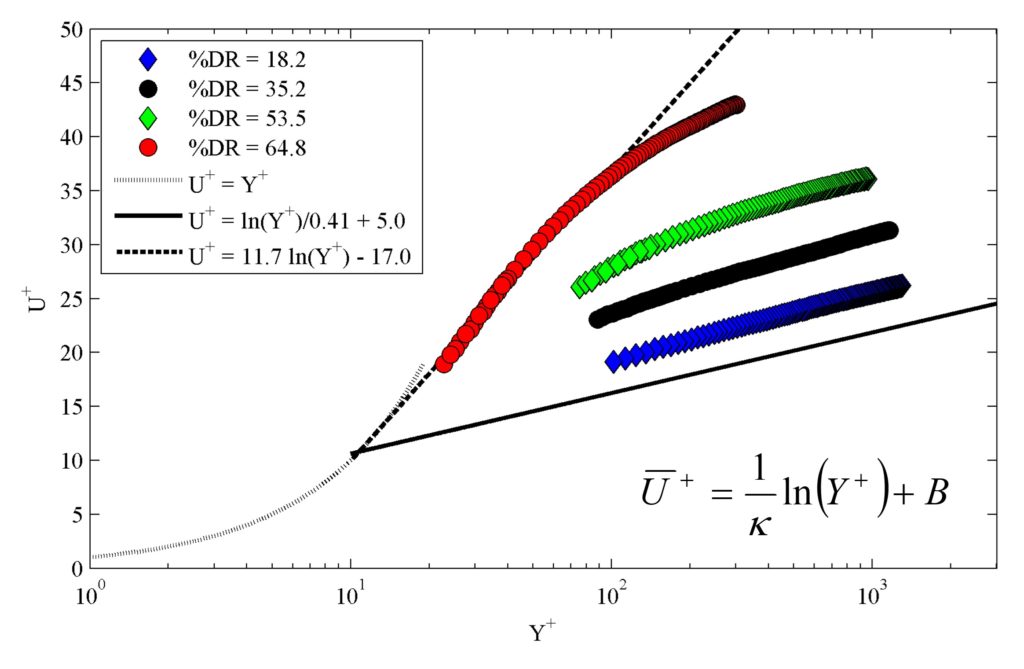
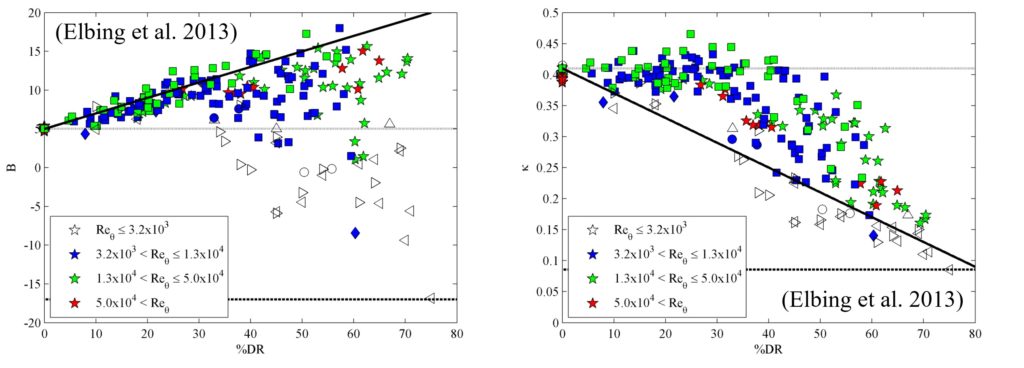
Even though it has been thought to be well understood for decades, recent numerical and experimental data have shown that the classical view of how drag-reducing polymer solutions modify the mean turbulent velocity profile is incorrect. The classical view is that the log-region is unmodified from the traditional law-of-the-wall for Newtonian fluids, though shifted outward into the flow (Virk, 1970). This outward shift is limited by what has been termed the ultimate profile, which is an empirically derived logarithmic profile. However, since the seminal work of Virk (Virk et al., 1970; Virk, 1975), there has been significant improvements in our ability to accurately measure velocities in wall-bounded flows. Consequently, numerous deviations from this classical view have been reported, though mostly dismissed due to the data being acquired at low Reynolds numbers where the log-region is small (i.e. difficult to determine the slope, especially in drag reduced flow which has a larger buffer region). The current project aims to reexamine the velocity distribution at high Reynolds numbers within wall-bounded polymer drag reduced flow. The long-term goal is to determine the functional dependence of the velocity profiles on flow and polymer properties as well as to assess its sensitivity to flow type.
Funding
BR Elbing (PI) “Modification of near-wall, high-Reynolds number velocity profiles with polymer solution,” NSF CBET Fluid Dynamics Program, No. 1604978, $297K, 3 years.
Related Publications
- BR Elbing, ES Winkel, MJ Solomon & SL Ceccio (2009) “Degradation of homogeneous polymer solutions in high shear turbulent pipe flow,” Experiments in Fluids, 47, 1033-1044 (doi.org/10.1007/s00348-009-0693-7).
- BR Elbing, DR Dowling, M Perlin & SL Ceccio (2010) “Diffusion of drag-reducing polymer solutions within a rough-walled turbulent boundary layer,” Physics of Fluids, 22(4), 045102 (doi.org/10.1063/1.3371957).
- BR Elbing, ES Winkel, SL Ceccio, M Perlin & DR Dowling (2010) “High-Reynolds-number turbulent-boundary-layer wall-pressure fluctuations with dilute polymer solutions,” Physics of Fluids, 22(8), 085104 (doi.org/10.1063/1.3478982).
- BR Elbing, MJ Solomon, M Perlin, DR Dowling & SL Ceccio (2011) “Flow-induced degradation of drag-reducing polymer solutions within a high-Reynolds number turbulent boundary layer,” Journal of Fluid Mechanics, 670, 337-364 (doi.org/10.1017/S0022112010005331).
- BR Elbing, M Perlin, DR Dowling & SL Ceccio (2013) “Modification of the mean near-wall velocity profile of a high-Reynolds number turbulent boundary layer with the injection of drag-reducing polymer solutions,” Physics of Fluids, 25(8), 085103 (doi.org/10.1063/1.4817073).
- BR Elbing (2018) “Flow-assisted polymer degradation in turbulent boundary layers,” AIChE Annual Meeting, Area 01C Interfacial Phenomena – Session 590e, Pittsburgh, PA (Oct 28 – Nov 2).
- Y Farsiani, Z Saeed, B Jayaraman & BR Elbing (2020) “Modification of turbulent boundary layer coherent structures with drag reducing polymer solution,” Physics of Fluids, 32(1), 015107 (doi.org/10.1063/1.5127293).
- Y Farsiani, Z Saeed & BR Elbing (2020) “Drag reduction performance of mechanically degraded dilute polyethylene oxide solutions,” ASME Journal of Fluids Engineering, 142(9), 091201 (doi.org/10.1115/1.4047118).
- BR Elbing (2020) “Comparison of turbulent boundary layer profiles modified with injection or uniform concentration of drag-reducing polymer solution,” ASME FEDSEM 2020, FEDSM2020-20317, virtual (July 13-15).
Resources
ELD 30-cm Water Tunnel
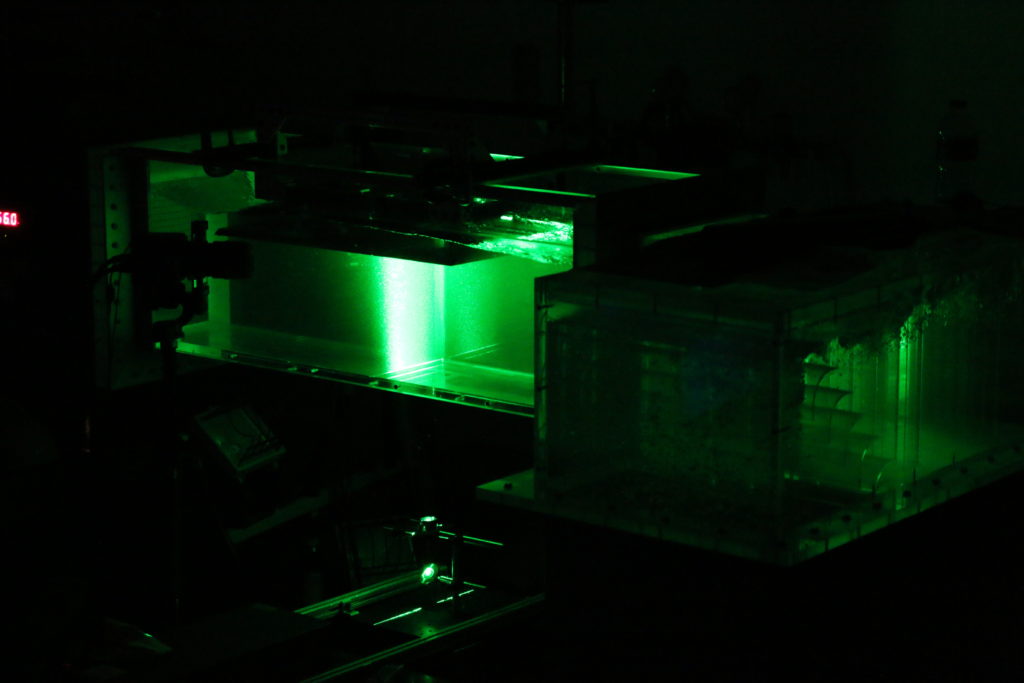
- Max speed = 1.1 m/s
- Test section: 0.3-m × 0.3-m × 1-m
- Model 503, Engineering Lab Design (ELD)
Virk Tubes
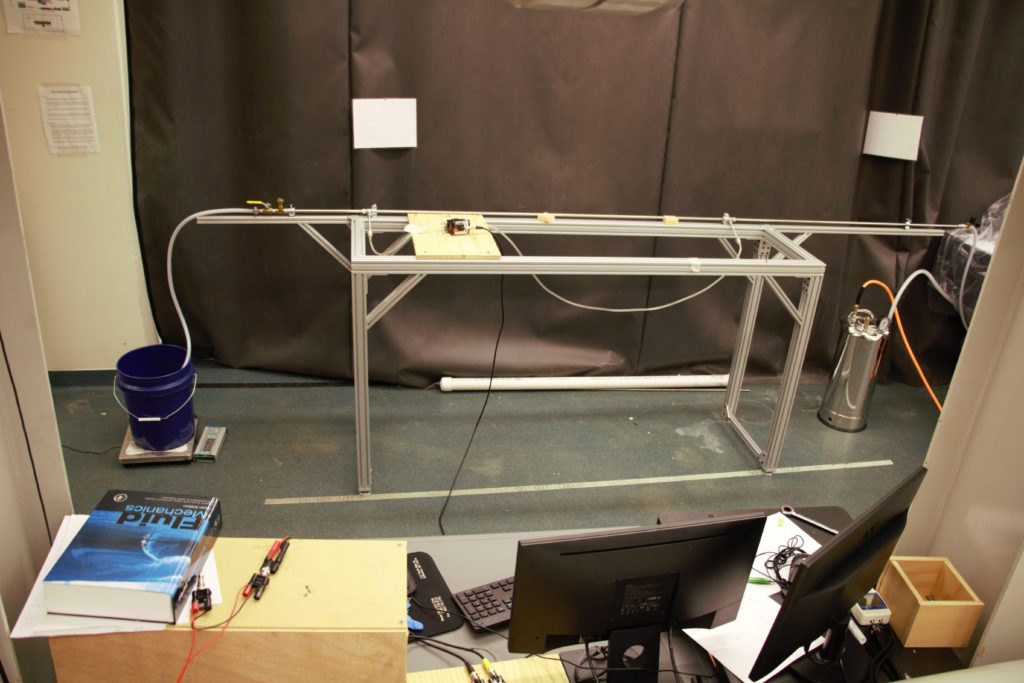
- Inner pipe diameters: 6.4, 9.5, and 12.7 mm
- Fully developed with ≥ 150 ID entrance length
- Driven via compressed air
Rheometer
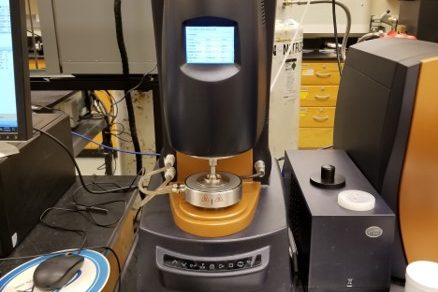
- DHR-2, TA Instruments
- Concentric cylinder, cone & plate (60mm, 2 degree), flat plates (8-mm, 20-mm)
- Shared with Dr. Aurelie Azoug
Petroleum Engineering Resources
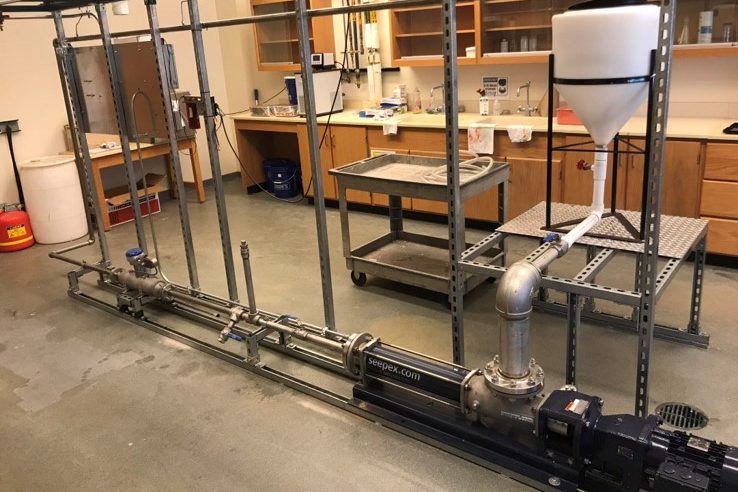
- Flow loops (up to 30 GPM)
- HPHT Rheometer
- Lubricity testing
- Temperature/shear controlled rheology microscopy
- Microfluidics based rheology & emulsion characterization
Flow Imaging
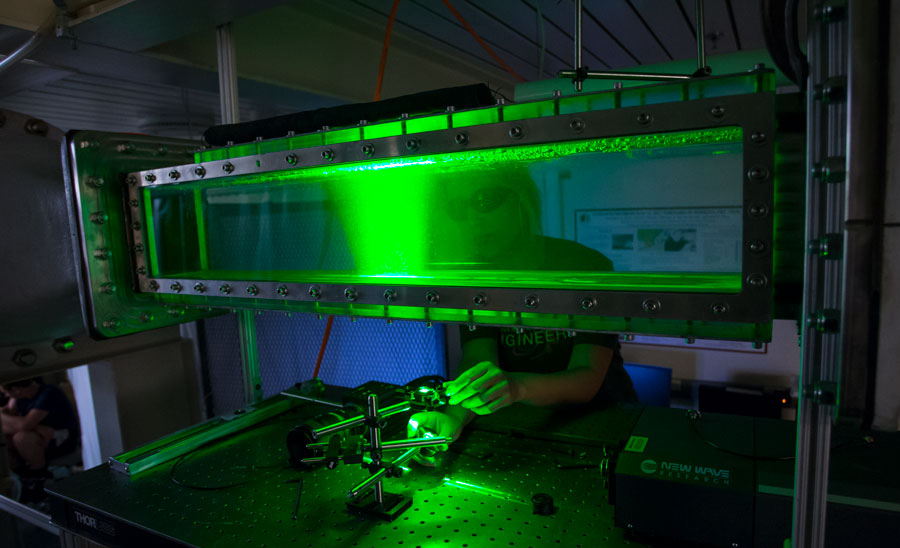
- Stereo-PIV, high-speed PIV, laser-induced-fluorescence (LIF), high-speed imaging
- Cameras: Phantom M110 (2×), LaVision Imager sCMOS (2×), HighSpeed-Star3
- Lasers: Photonics DM30-527, New Wave Gemini 200, Big Sky Ultra50